|
|
DPI School Bus Delivery Team Honored Recipients
of
Team Excellence Award
|
DPI Human Resources Director Jack Stone presented the first DPI Team Excellence award to "Bus Replacement Team" members Charles Ball, Steve Beachum, Kevin Harrison, James Hawkins, Randy Henson, Jean Strickland and Craig Warren. Their nomination resulted from the exemplary way in which, as a result of this team’s efforts, DPI was able to successfully assist LEAs with the procurement and delivery of 1360 new school buses prior to the start of school. |
DPI Human Resources Director Jack Stone presented the first DPI Team Excellence award to Transportation Services team members Charles Ball, Steve Beachum, Kevin Harrison, James Hawkins, Randy Henson, Jean Strickland and Craig Warren. Their nomination resulted from the exemplary way in which, as a result of this team’s efforts, DPI was able to successfully assist LEAs with the procurement and delivery of 1360 new school buses prior to the start of school.
Team Camaraderie
PLEASE NOTE: The SCHOOL BUS DELIVERY TEAM from DPI Transportation Services was responsible for making sure that all public school buses in the state were replaced. This year, 1360 new school buses are going into service in nearly all LEAs. This line of buses would run from the Education Building in downtown Raleigh past Triangle Towne Center in North Raleigh! This particular project required transportation staff with varying responsibilities to come together to get school buses for 2007 (over 90% of them financed) to the LEAs.
Information systems, financing, communication and final inspections of these 1360 vehicles required the talents of no less than 7 DPI staffers. Charles Ball chaired the specifications committee and James Hawkins and Randy Henson also served on this committee, which was responsible for developing bus specs. Craig Warren served as liaison between the spec committee and the Dept. of Administration Division of Purchase and Contract. Steve Beachum coordinated the financing of the buses. Kevin Harrison created a computer application to run on ruggedized laptops so that staffers could record defects found during the acceptance inspection of each vehicle. Jean Strickland coordinated the communication with LEAs to ensure that the right LEAs showed up for each of the 11 deliveries of replacement school buses. |
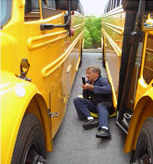
Charles Ball inspects the chassis on a creeper.
|
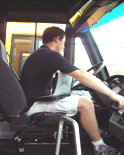
Kevin Harrison cranks the engine on a new school bus. |
This final acceptance inspection required the cooperation and hard work of each member of the team. At least 120 man-days (that’s 6 months!) were spent by the DPI team, with assistance from others, primarily LEA spec committee members. These folks supported each other, covered for each other during vacations and performed duties outside their work plans in order to complete the mission.
Despite 95 degree days on hot asphalt, crawling under buses, inspecting inside buses and checking under the hood – no one complained, because at the end of each day, there was a universal feeling that the work resulted in a higher quality and safer school bus for students in North Carolina. |
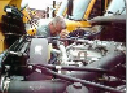
Craig Warren inspects the engine compartment.
|
|
Building Partnerships with Customers
Customers had an opportunity to work with all team members in the course of purchasing, inspecting and delivering the new school buses. Internal and external relationships were strengthened:
LEAS: Despite obstacles early on in the process, an aggressive schedule was put in place so that all LEAs received their school buses before school started. LEAs received reports, for the first time, of defects found prior to delivery of new vehicles.
VENDORS: The school bus vendors – Thomas and International – were provided with computerized reports that showed the defects of each school bus prior to delivery. This report was also given to the LEA so that they knew what to look for. Further, the team worked side by side with bus company personnel in making sure that all defects were identified and corrected prior to delivery.
DPI and FINANCE COMPANIES: DPI staff in Financial and Business Services that deal with LEAs and the allotment of funds had to process quite a bit of information, that was gathered by this team and provided in a timely and orderly fashion – week after week during the delivery time. A contract for 3rd party financing was carried out so that all payments for buses were made upon acceptance and delivery of the buses.
Innovative Thinking
One of the key innovations in this project was the development and use of a computer application. It was adapted from the application used by the field consultants for inspecting school buses during the school year. The data contained in the application were forwarded to the vendor for defect correction. The data were also forwarded to the LEAs so they could double-check to see that defects were corrected and to keep an eye on things as the buses go into service. For instance, if an inspector found a new bus that wouldn’t start, it may have simply resulted from a light being left on. However, if it became a recurring problem, the LEA would want to know that this was an identified problem immediately after the bus was manufactured, as there may be a more serious problem. |
|
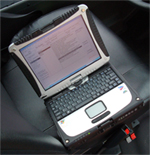 |
There was continuous feedback between the staff inspecting the new buses and the programmer (Kevin) so that the application became more useful for DPI staff and the customers each time a batch of buses was inspected and delivered.
As the deliveries were processed and Steve worked with LEAs on acceptance and financing documents, the application data were integrated in the paper flow. Steve, Kevin and Jean coordinated all of the documents. Craig and Kevin collaborated on the input data. James, Charles, Randy and Kevin collaborated on the flow of the application.
Dedication to Excellence
This team worked with the 11th delivery of replacement school buses with the same determination as the 1st delivery. Every time a correction was needed – no matter how minute or important – the team made sure that it was completely documented to ensure that the bus was delivered in the condition that the team is proud to endorse.
The team understood that the details of inspection, delivery and financing were critical to the success. This attention to detail never wavered, even as the team proceeded through the 11th delivery.
One of the inspection processes is to compare the 17 digit VIN # in the computer system with the metal tag containing the VIN mounted under the hood on the firewall and the same VIN # embossed on a metal plate mounted to the interior ceiling about the driver’s head. On the last delivery of buses – which took place on July 31 – there were five buses in which the team found mismatches of ONE digit within that VIN # and new tags had to be produced and installed. Without this dedication to excellence, conflicting identifying fleet information would be on different parts of the vehicle. This is just one example.
Dedication to Service
The most time consuming part of the vehicle delivery project was the inspection and reinspection of each and every school bus. Even though these buses are brand new, not everything is always 100% correct with them. The detail associated with each one shows the high level of service to which the entire team was dedicated:
- Team is notified by vendor that buses are ready for inspection
- Send preliminary delivery list to LEAs receiving buses
- Prepare financing documents
- Conduct inspection of new school buses – 2 man team (about 30 buses/day)
- Inspect inside engine compartment
- Validate VIN numbers under hood and above driver with database
- Verify that the vehicle is full of fuel for the LEA
- Verify that the length of bus (student capacity) is correct and labeled
- Ensure that there are no sharp edges, exposed screws, etc in student area
- Inspect under the bus to ensure proper brake linings and identify defects
- Inspect under the bus to ensure that the air conditioning is properly charged
- Inspect inside bus to ensure all switches work, proper seating configurations
- Check lights, stop sign and crossing arm operation
- Send database of defects to vendor
- After 1-3 days, perform re-inspection to ensure all defects were corrected
- Consult regularly with vendor to address problem issues
- Send final list of buses to LEAs
- Contact each county to make sure they will be at the delivery at the appointed time
- Finalize financing documents and have prepared for LEA signature.
- Meet LEAs at vendor facility on delivery day to process delivery of vehicles
- Update new buses in fleet maintenance system
- Fax all financing documents to finance company
- START OVER AGAIN with the next batch of 100+ buses.
Ultimately, the LEA is the customer. They cut the purchase order and are responsible for the financing contract. They have to make sure that each bus is ready to run to serve the students of North Carolina. The tasks performed by the School Bus Delivery Team were aimed toward a single goal: Providing the maximum service to the LEAs prior to the delivery to ensure that the time from bus delivery until students are picked up is as carefree as possible.
The 120 man-days required and the volume of this particular school bus acquisition (1360 buses) made this project particularly challenging. Even on the hottest days and the processing of paper after paper, the team kept going, with an eye on excellence for one reason: Serving the LEAs. Team members supported each other and worked shoulder to shoulder, each member bringing his/her expertise. Because they are ALWAYS willing to support each other and pull together, even a project of this magnitude was do-able, successful and even enjoyable. And very rewarding to each member of the team.
LEA Involvement
The team offers special thanks to the following spec committee members and other “recruits” that spent time and sweat in participating in the inspection of new buses:
- Reid Cagle, Lee County
- Ricky Whaley, Greene County
- Keith Whitley, Nash-Rocky Mount
- Art Collier, DMV
- Curtis Hodge, Rutherford County
- Bobby Taylor, Brunswick County
- David Twiddy, Dare County
- Billy Smith, Randolph County
- Jay Temple, Davidson County
- Terry Barlow, Wilkes County
- Rick Jennings, Wilkes County
- Mickey Michael, ITRE
- Robert Boggs, Iredell County
- Terry Campbell, Iredell County
|
|
|
|