A career as an automotive or heavy duty vehicle technician is ranked as one of the more hazardous occupations. It is paramount that all lifting equipment used under the vehicle, for elevation to any height, be understood and used properly before a technician ventures under a lifted vehicle at any level. Equally hazardous are the use of pits, which by their simple existence become permanent trip hazards. |
|
|
It is a common misnomer that the use of a floor jack or a bumper jack allows for a safer scenario for the technician because one is limited to less elevation. This is simply not so. It should be also noted that steel on steel pick-points make a lifted vehicle more vulnerable, especially on a slant where an unlevel vehicle and floor plane accompanied with a gravitational pull can force the vehicle off of its perch.
|
Statistics don’t lie
While some accidents are attributable to improper installation or poor manufacturing, accidents related to improper operator use are the most common reason for injury or death while operating lifting equipment. According to Service Tech Services, a lift safety inspections company in Simi Valley, Calif., more than 15,000 accidents causing death or hospitalization occur every year from lift-related accidents.
Lift accident injures N.C. bus garage employee
Four years ago a Lincoln County School transportation employee was changing a tire on a transit style bus when something caused the bottle jack he was using to shift. The bus fell on his hip area and pinned him under the bus for nearly 10 minutes. The bus technician suffered internal injuries as well as a broken hip. Luckily an EMT crew was nearby visiting the school he was working at. His outcome could have been much worse had there not been a quick response. “As of 2011 he is still disabled and unable to return to his job with the bus garage” reports Eric Eaker, Lincoln Co. Transportation Director.
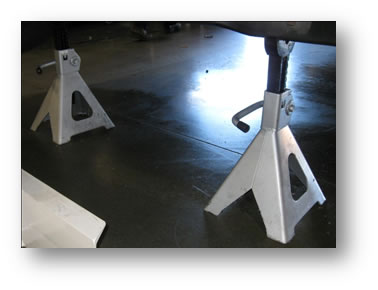
Jack stands are essential safety insurance and their use must not be neglected
In-Floor lifts are a very safe option but must be maintained annually
Safety first
One of the greatest safety resources available to those who operate vehicle lifts is the Automotive Lift Institute (ALI). The ALI is an association of lift manufacturers focused on promoting safety in the design, construction, installation and use of lifts.
The ALI sponsors a “Program of Certification” for lifts through a contract with Intertek Testing Services, a worldwide testing organization recognized by OSHA.
The ALI recently released a new “Safety Tips” placard, which describes general safety precautions that should be taken to help avoid injuries. The placard, which can be ordered through ALI’s Website, www.autolift.org, should be posted where it can be a constant reminder to lift operators. Here are the 11 safety tips:
1. Inspect your lift daily. Never operate if it malfunctions or if it has broken or damaged parts. Repairs should be made with original equipment parts.
2. Operating controls are designed to close when released. Don’t block open or override them.
3. Never overload your lift. Manufacturer’s rated capacity is shown on nameplate affixed to the lift.
4. Positioning of vehicle and operation of the lift should be done only by trained and authorized personnel.
5. Never raise vehicle with anyone inside it. Customers or bystanders should not be in the lift area during operation.
6. Always keep lift area free of obstructions, grease, oil, trash and other debris.
7. Before driving vehicle over lift, position arms and supports to provide unobstructed clearance. Do not hit or run over lift arms, adapters or axle supports. This could damage lift or vehicle.
8. Load vehicle on lift carefully. Position lift supports to contact at the vehicle manufacturer’s recommended lifting points. Raise lift until supports contact vehicle. Check supports for secure contact with vehicle. Raise lift to desired working height. Caution: If you are working under vehicle, lift should be raised high enough for locking device to be engaged.
9. Note that with some vehicles, the removal (or installation) of components may cause a critical shift in the vehicle center of gravity and result in raised vehicle instability. Refer to the vehicle manufacturer’s service manual for recommended procedures when vehicle components are removed.
10. Before lowering lift, be sure tool trays, stands and other equipment are removed from under vehicle. Release locking devices before attempting to lower lift.
11. Before removing vehicle from lift, position arms and supports to provide an unobstructed exit.
Make sure that technicians receive training & review directions
There is consensus among manufacturers that training for technicians is paramount to understand how to safely operate vehicle lifts. At a basic level, manufacturers recommend that technicians read the lift’s owners manual from cover to cover to become familiar with its safety features and how to operate the lift.
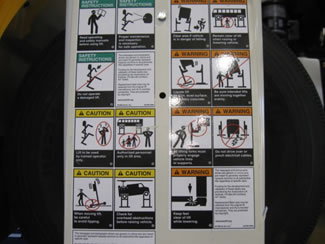
Follow instructions attached to the equipment.
Inspect vehicle lifts regularly
Just as school buses must be inspected and maintained on a regular basis to function properly, vehicle lifting equipment should be inspected annually to make certain that they are well maintained and operating correctly. The inspection should involve first reviewing safety material provided by the manufacturer of the lifting equipment.
OPEN PITS
An uncovered pit can quite easily become the
site of an accident, leading to a fall and serious
injury.
REDUCING THE HAZARDS
* Some establishments provide sectionalised
guard-railing designed to slip into prepared
floor sockets to prevent the unwary from
walking into exposed pits. Others suspend
chain from removable steel uprights to
achieve the same result. These provide a
measure of safety only if erected when a pit
is open.
* The ideal pit guard is one that is
constructed of heavy interlocked steel
plates designed to run smoothly and easily
through guide rails in the manner of a roller
shutter door.(see pic) |
|
Swain Co. has installed OSHA approved safety grate |
When quality certified lifting equipment is used properly, garages should actually see a decrease in accidents, in comparison with shops where more traditional equipment is being used. Also, with the proper use of lifts, workman’s comp. incidences, related to poor ergonomics, will decrease due to the fact that work can easily be adjusted to levels less conducive to bodily strain. By the same token greater productivity can be achieved as there is less waste of motion and reduced rework.